Removing The Cross Slide Dial Bearing Block
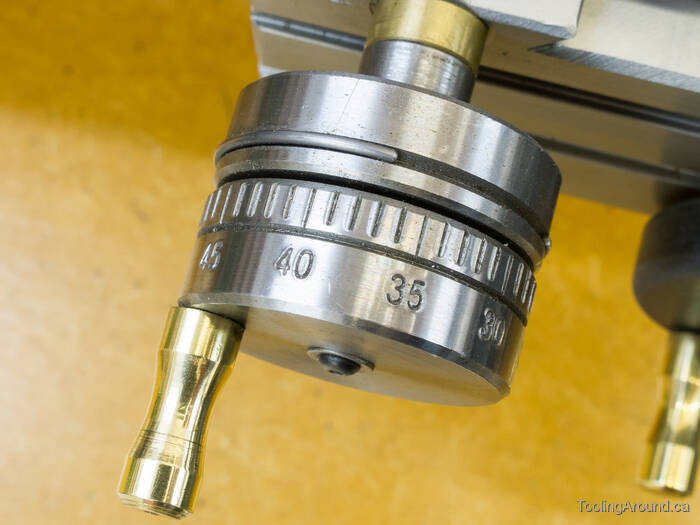
Sometimes, it's necessary to remove the cross slide dial bearing block while servicing the lathe. At first glance, it's not obvious how this is done. Look at the backside of the bearing block, however, and you'll see a clue.
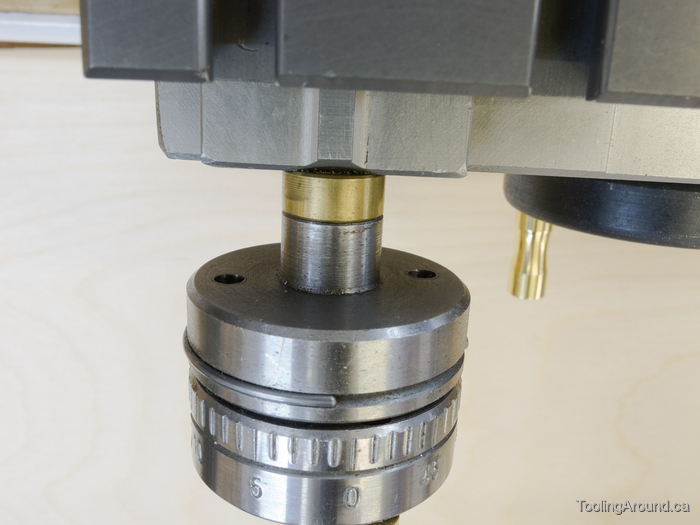
Well, there are two clues, actually, and they're both holes. They're intended for a pin wrench. Here are the business ends of two such wrenches.
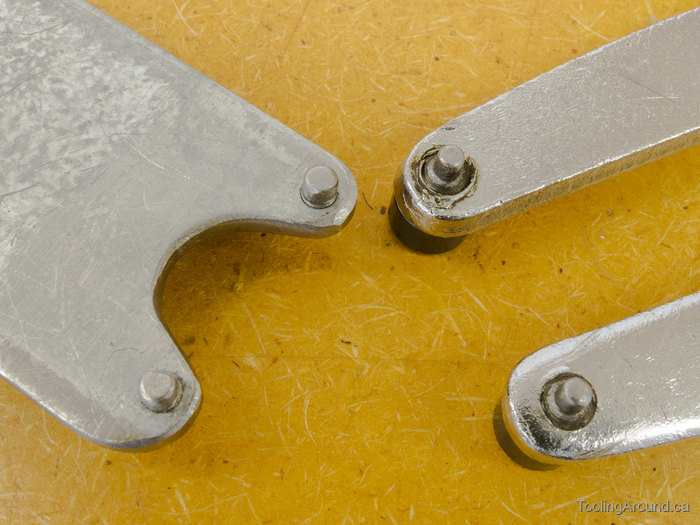
The one on the right is a commercial product and the other is shop made. Which you need will depend on whether you have the old-style carriage, made from a casting, or the new-style carriage, made from an extrusion. When choosing which to buy (or make), the important thing is the distance between the back of the bearing block and the carriage.
On either bearing block, the distance between the hole centres is 0.875″. A suitable pin diameter is 0.1″.
New-Style Carriage (Skip to "Old-Style Carriage".)
On my new-style carriage, the distance between the back of the bearing block and the carriage is 0.48″.
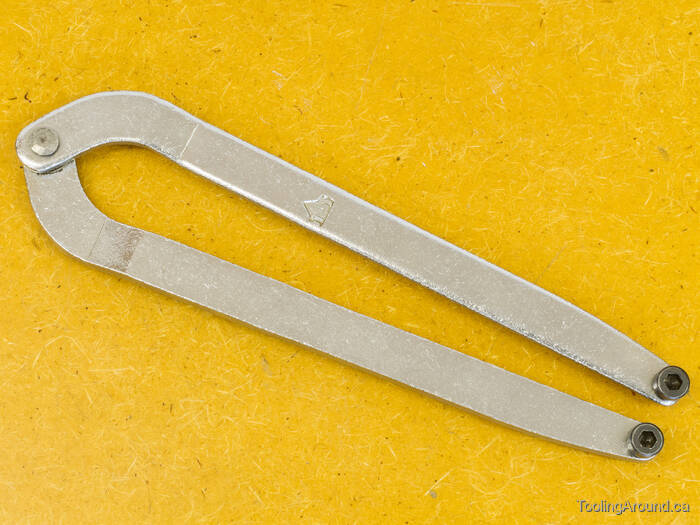
This is an example of an inexpensive pin wrench. At one end, there's a pivot that allows you to change the distance between the pins at the other end.
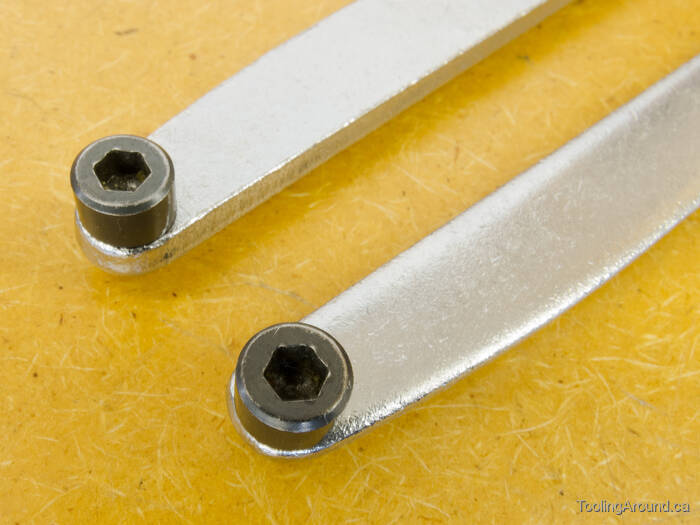
On this wrench, the pins are made from a pair of SHCS's.
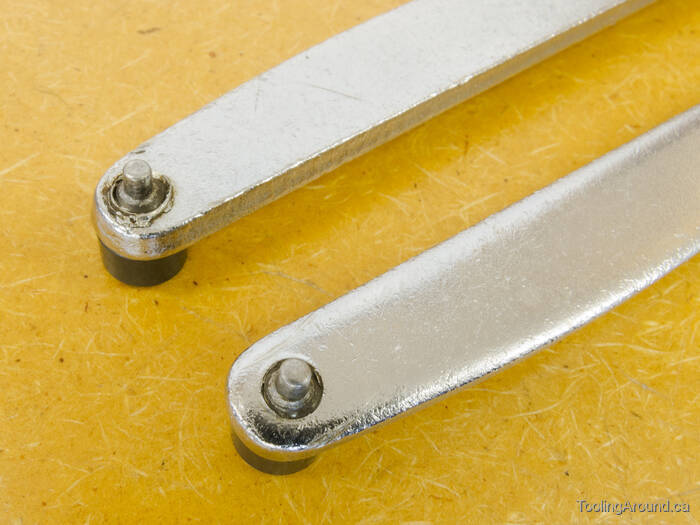
The ends of the SHCS's were turned down to make the pins.
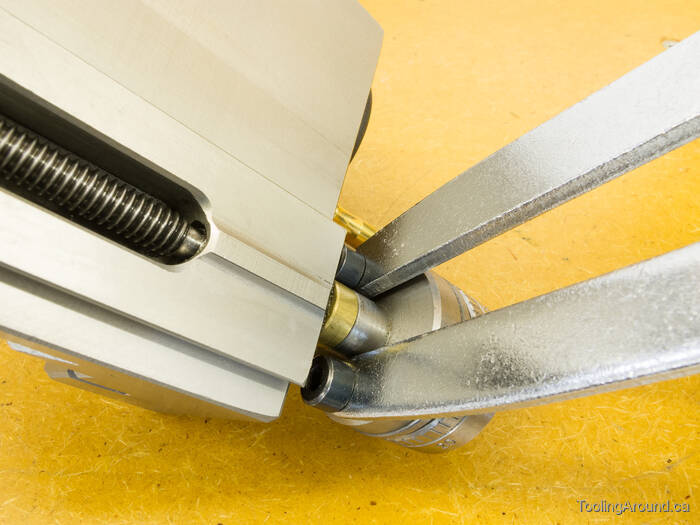
The wrench is in position, ready to remove or tighten the bearing block.
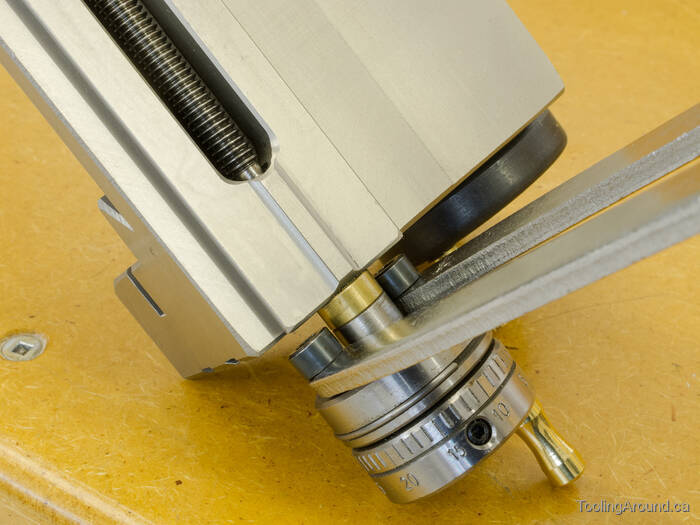
You can clearly see how much space there is, above the screw head.
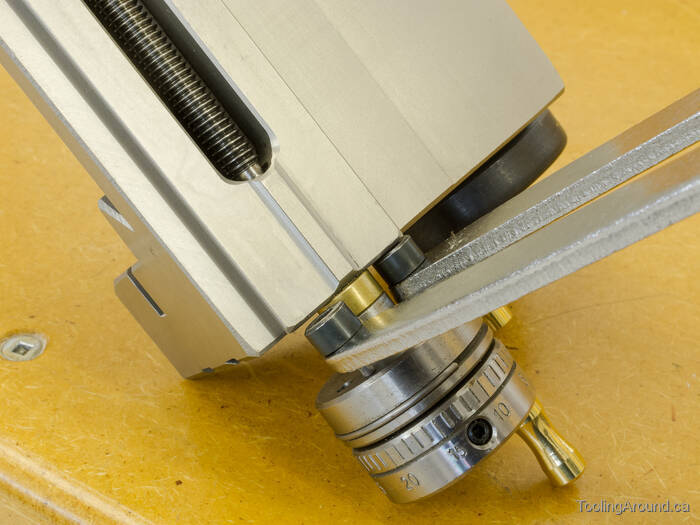
With the pins clear of the hole, there's enough room to remove the wrench.
Old-Style Carriage
On my old-style carriage, the distance between the back of the bearing block and the carriage is 0.27″.
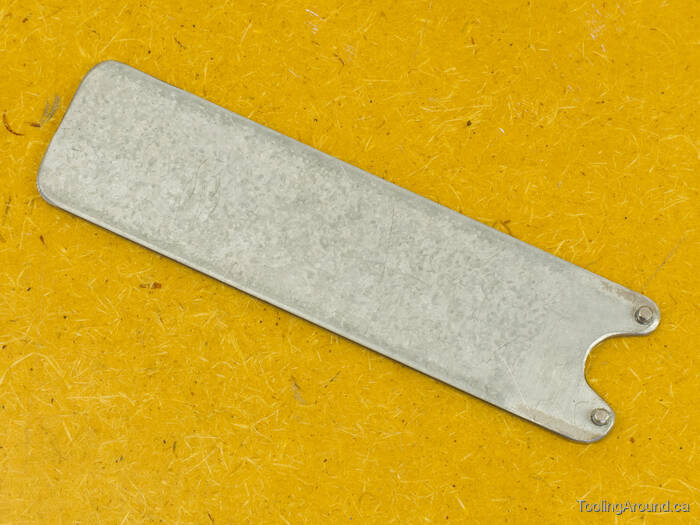
Here's a simple pin wrench, made from a scrap of steel strap. It measures 1.26″ wide by a bit under 5″ long, 0.11″ thick.
It's almost embarrassing to provide a photo of this rather crude wrench. Admittedly, it was made in a hurry, but it serves its purpose.
The pins are bits of steel rod, projecting 0.1″ from the surface of the bar. I measured the diameter as 0.1″, but if you make one, all you have to do is make sure they fit the holes in the bearing block.
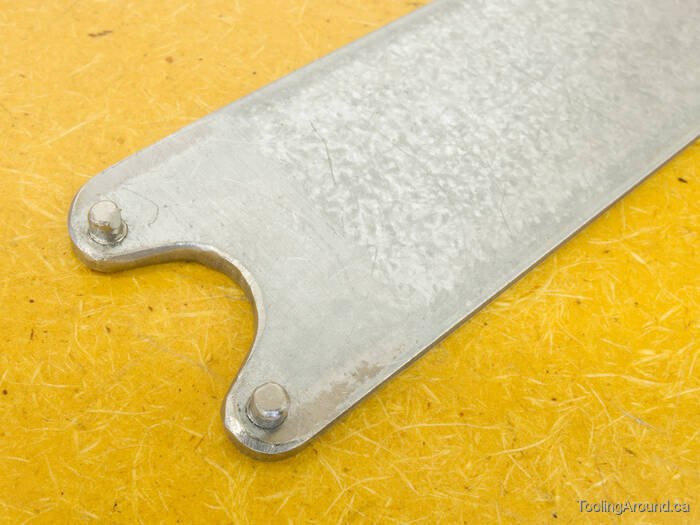
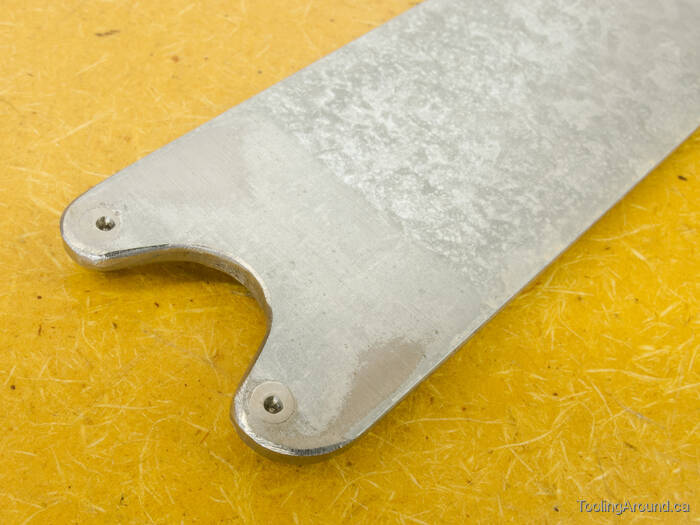
The pins are a close fit in holes drilled in the bar. To fix them in place, I used a firm blow on a centre punch to displace the metal, expanding it in the hole. Afterwards, I smoothed the rough edges on my 1″ belt sander.
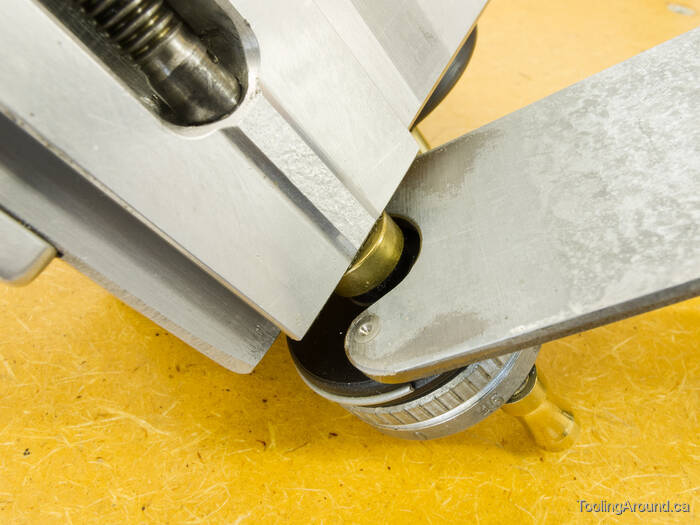
Here's how it looks in action.
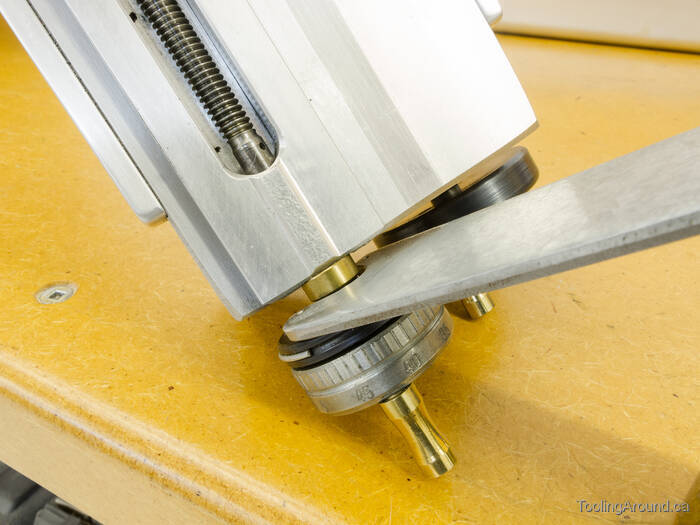
For this wrench, there's plenty of clearance. The other wrench is much too big to fit in the available space.